Summary of all activities of Metallic Construction Materials group is here .
For weathering and climatic tests (degradation by UV and other climatic factors), click here.
Accelerated corrosion and weathering tests are useful tools for material selection, initial and residual life time prediction of bare and painted metallic, polymeric, adhesive and other materials in atmospheric exposure conditions and quality control. It is widely used in the automotive, aerospace, building, off-shore, military and infrastructure applications.
Beside generally known Neutral Salt Spray (NSS), Acetic Acid Salt Spray (ASS) and Copper-Accelerated Acetic Acid Salt Spray (CASS) tests, a number of modern cyclic corrosion tests including wet and dry phases has been developed. Because of more realistic conditions, their results correlate better to those from natural exposures and thus provide significantly improved predictive ability. The traditional NSS and its variants are more suitable for quality control.
![]() |
![]() |
![]() |
In our advanced automated corrosion chambers with a volume of 2000 and 1000 liters with temperature control from –40 to 80 °C and control of the relative humidity (RH) from about 20 to 100 %, we are able to perform tests according to most international, national and industrial standards for commercial applications and research purposes.
Cyclic corrosion tests
VDA 233-102, SEP 1850, EN ISO 11997-3 (N-VDA)
This test has been created jointly by a group within the German Association of the Automotive Industry, VDA, with the aim to serve for the development of new materials and coatings. It allows for the assessment of the corrosion behaviour of components and of the corrosion protection provided by coating systems for applications in the automotive industry. The accelerated test covers in particular the delamination around a defined artificial defect in a coating as well as surface and cut edge corrosion on special test panels, bonding specimens or components. This laboratory-scale cyclic corrosion test is also suitable for assessing perforation corrosion in flanged areas or gaps (hem flanges) and of unpainted surfaces. This method induces corrosion processes and generates reproducible corrosion patterns which correlate well with the results obtained in natural weathering tests and driving operation. In particular, the corrosion patterns for steel, galvanised steel and aluminium closely reflect real-life phenomena. The test method is based on real corrosive climate conditions and delivers differentiated results for a large number of uses in automotive applications. |
![]() |
Conditions: Complex test including a variety of technical phases such as a salt spray phase (1 wt.% NaCl solution, pH neutral), wet and dry cycles at temperatures up to 50 °C and a freezing phase at –15 °C. Typical duration: 6 weeks. A week cycle is shown in the chart.
VW PV 1210 (Volkswagen Group)
This method is designed for corrosion testing of automotive materials conducted on completely painted bodies, body panels, assemblies and add-on parts with differing corrosion protection coatings. It serves to monitor and evaluate corrosion behaviour or corrosion protection measures when exposed to static load. Conditions: 5-day cycle comprising of NSS (35 °C, 5 wt.% NaCl solution), dry phase and humid phase at 40 °C and 100% RH followed by 2-day rest at laboratory temperature. Typical duration: 3, 6, 12 or 18 weeks. A week cycle is shown in the chart. |
![]() |
VW PV 1209 (Volkswagen Group)
Conditions: Combination of the PV 1210 with cycles of rapid variations of temperature and RH from –40 to 80 °C and from 30 to 80 % RH. The chloride solution used for salt spraying is modified and contains 4 wt.% NaCl and 1wt.% CaCl2.
The high/low temperature cycle is designed for testing vehicle parts in the engine compartment in view of e.g. susceptibility to cracks, deformation, separation of the composite material, etc. It can be informative in view of paint stability as well.
Volvo STD 423-0014, VCS 1027,149 (ACT I), Scania STD 4319
This test procedure is designed for assessment of corrosion resistance in environments with a significant effect of chloride ions, in particular in marine climates and in regions where de-icing salts are applied in winter for road treatment. It is used for metals and their alloys and metallic, conversion and organic coatings. In contrary to most other procedures, salt solution is applied in a form of rain with the deposition intensity of 15 mm/hour. Six weeks of the test simulate about 2 years of service in an area where de-icing salts are used during winter. Conditions: Two times a week, samples are shortly contaminated with 1 wt.% sodium chloride solution acidified with sulphuric acid to pH 4.2. Wetting (35 °C and 95 % RH) and drying (45 °C and 50 % RH) cycles are altered for the rest of the time. A week cycle is shown in the chart. |
![]() |
Volvo STD 423-0069, VCS 1027,1449 (ACT II), Ford CETP 00.00-L-467
Salt solution is applied five times a week in a form of rain by an automatic device or, if it is not available, manually. Six weeks of the test corresponds to 2-4 years of car service in areas where de-icing salts are used. This method differs from ACT I in folowing aspects: (1) The corrosion rate for steel is approximately 50 % higher with respect to paint undercutting in confined mode (crevices, etc), but only 10 % higher for general corrosion in open mode; (2) The corrosion rate for zinc is in the order of 30 % lower for open corrosion, but 10-30 % higher for under-paint corrosion of galvanized steel; (3) The test method in this standard is applicable to painted aluminium, contrary to ACT I; (4) This method is better suited to corrosion testing of magnesium (due to longer time of macro wetness), especially when under bimetallic influence; (5) This test is less efficient regarding pitting of aluminium and staining of anodized aluminium, due to the lower frequency of humid to semi-dry cycles; (6) Austenitic stainless steels may exhibit exaggerated red rust due to the comparatively high exposure temperature combined with cyclic drying (above critical pitting temperature). Conditions: Five 24-hour workday cycles comprise each of 6-hour wet phase at 25 °C with intermittent exposure to 0.5 wt.% sodium chloride solution, 2.5-hour transition drying period and 15.5-hour phase with constant temperature and humidity of 50 °C and 70 % RH. The same conditions are maintained during weekends. |
![]() |
Nissan CCT I (CCT 1)
Conditions: Repetition of 8-hour cycles with 4 hours of NSS (35 °C, 5 wt.% NaCl solution), 2 hours of drying at 60 °C and RH < 30 % and 2 hours of moistening at 50 °C and 95 % RH. Typical duration: 500 to 1500 hours.
Nissan NES M0158 (CCT IV, CCT 4)
Conditions: Repetition of 24-hour cycles with 4 hours of NSS (35 °C, 5 wt.% NaCl solution), 2 hours of drying at 60 °C and RH < 30 % and 2 hours of moistening at 50 °C and 95 % RH followed by 5 wet/dry cycles at constant temperature of 60 °C
Renault ECC1 D17 2028
Conditions: Test performed at constant temperature of 35 °C and comprising wet (90 % RH) and dry (55 % RH) phases. Sodium chloride solution with 1 wt. % NaCl at pH 4 is sprayed over samples during 30 minutes once a day followed by a drying phase at 20% RH. Typical duration: 6 weeks.
Toyota TSH1555G, Method C
The test procedure reproduces corrosion conditions on car bodies. |
![]() |
PSA TCAC D13 5486 (Peugeot, Citroën)
Conditions: Salt spray with 1 wt.% NaCl solution at pH 4.1 and wet and dry cycling at a constant temperature of 35 °C.
BMW AA-0224 (PA-P 029)
Conditions: A day of salt spray at 35 °C, 4 days of intermittent condensation at 40 °C and repose in laboratory air and 2 days of repose.
Fiat 50493/05
Conditions: A cycle comprises of 3 hours of salt spray at 35 °C, 1 hour of drying at 60 °C, 12 hours of wet conditions at 95 % RH and 40° C, 1 hour of freezing at –10 °C and 6 hours of repose at 25 °C and at 60 % RH.
SAE J-2334, GM 954OP, GMW 14872
Procedure used throughout the North American (GM group) and Japanese (Suzuki, Mitsubishi) automotive industry. Since it is a field-correlated test, it can be used as a validation tool as well as a development tool. If corrosion mechanisms other than cosmetic or general corrosion are to be examined using this test, field correlation must be established.
Conditions: Test specimens are exposed to a changing climate that comprises of three repeating sub-cycles of 24 hours in total: 6 hours exposure to a water fog/condensing humidity at 50 °C; 15 minutes immersion in or a direct spray of salt water at ambient conditions; and air drying at 50 % RH and 60 °C. The contamination solution contains NaCl, CaCl2 and NaHCO3.
JSAE JASO M 609, JASO M 610, ISO 14993, EN ISO 11997-1 Cycle A
A procedure designed for bare, metallic coated and painted steel panels for use in the automotive industry and elsewhere. Paint system degradation is evaluated using the set of standards EN ISO 4628.
Conditions: Repetition of cycles of salt spray with neutral 5 wt.% NaCl solution at 35 °C (2 hours), drying phase at 60 °C and at 20–30 % RH (4 hours) and wetting condensing phase at 50 °C and at 95 % RH (2 hours). Typical duration: 30–180 cycles (240–1440 hours).
VDA 621-415, EN ISO 11997-1 Cycle B
The predecessor of VDA 233-102. Due to high chloride load, the test provides rather unrealistic results for non-protected metals comparable to those in NSS. It is used for testing of thermally cured paint systems for automotive applications.
Conditions: 1 day of NSS (35 °C, 5 wt.% NaCl solution), 4 days of wet (40 °C / condensation) and dry (23 °C / 50 % RH) cycling, 2 days at laboratory temperature and RH. Typical duration: 5 weeks (ISO) or 10 weeks (VDA).
ISO 16701 (CCT)
Conditions: Humidity cycling between 95 and 50 % RH at 35 °C with 6-hour salt spray sub-cycle carried out twice a week. The sub-cycle consists of 3 cycles of 15-minute spraying with a 1 wt.% NaCl solution acidified to pH 4.2 followed by a 105-minute period of wet stand-by.
The low pH level of the spraying solution simulates acidic precipitation present in industrialized areas.
ASTM D 5894
Cyclic corrosion and UV exposure of paints on metal using alternating periods of exposure in two different cabinets: a cycling salt spray/dry cabinet and a fluorescent UV/condensation cabinet.
Conditions: The fluorescent UV/condensation cycle is 4-hour UV at 0.89 W m–2 nm–1 at 340 nm and at 60 °C and 4-hour condensation at 50 °C. The salt spray/dry chamber runs a cycle of 1-hour salt spray at ambient temperature and 1-hour dry-off at 35 °C. The salt spray electrolyte contains 0.05 wt.% sodium chloride and 0.35 wt.% ammonium sulphate.
ASTM G 85, Practice A2 (Cyclic Acidified Salt Fog Testing
Modifications of NSS with humidity cycling and altered spraying solution.
Conditions: Six-hour repetitive cycles of 45 minutes of spraying with acidified 5 wt.% NaCl solution, 120 minutes of drying and 195 minutes of exposure to high RH.
ASTM G 85, Practice A3 (Acidified Synthetic Sea Water (Fog) Testing)
Modifications of NSS with humidity cycling and altered spraying solution. This test is particularly useful for production control of exfoliation-resistant heat treatments for the 2000, 5000, and 7000-series aluminium alloys. It is also applicable to developmental studies of varying heat treatment parameters to determine effect on corrosion behaviour. For this purpose, a temperature of 49 °C is recommended for the exposure zone. For testing organic coatings on various metallic substrates, an exposure zone temperature of 24 to 35°C may be used since temperatures in excess of 35°C frequently result in paint blistering.
Conditions: Two-hour repetitive cycles of 30 minutes of spraying with acidified artificial sea water and 90 minutes of exposure to elevated RH.
ASTM G 85, Practice A5 (Dilute Electrolyte Cyclic Fog/Dry Test, Prohesion)
Prohesion is a shortened form of “protection is adhesion”. It was designed for paints on steel and believed to be somewhat more representative of outdoor corrosion than NSS. Prohesion testing has been found especially useful for industrial maintenance coatings.
Conditions: Short cycles of 1-hour spraying with a diluted solution of sodium chloride (0.05 wt.%) and ammonium sulphate (0.35 wt.%) at pH 5–5.4 and 1-hour dry-off.
EN ISO 11997-1 Cycle C
A test developed for water based and latex paint systems.
Conditions: Repetition of phases of salt spray deposition made of sodium chloride (0.31 g/L) and ammonium sulphate (4.10 g/L) at 30 °C, drying at 40 °C, wetting at 40 °C and 75 % RH, drying at 30 °C and condensation at 30 °C. A cycle takes 48 hours and the whole test includes 21 cycles (1008 hours).
EN ISO 11997-1 Cycle D, JIS K 5621
A test for paint systems.
Conditions: 30 minutes NSS (30 °C, solution of 5 wt. % NaCl), 90 minutes high humidity (30 °C / 95 % RH), 120 minutes hot dry (50 °C), 120 minutes warm dry (30 °C). This 6-hour cycle is repeated 28 times. The whole test takes 168 hours.
EN ISO 11997-2
The test cycle includes a phase of salt fog deposition, drying, wetting, and exposure to UV irradiation. It is suitable for industrial air-curedpaint systems for protection of steel structures.
Conditions: Samples are places into a UV chamber according to requirements of EN ISO 16474-3 with UVA 340 lamps. The cycle consists of UV irradiation at the black object temperature of 60 °C (4 hours) and condensation at 50 °C (4 hours). After 168 hours in the UV chamber, samples are transferred to a cyclic corrosion testing chamber for another 168 hours. The corrosion cycle consists of salt spray deposition made of sodium chloride (0.5 g/L) and ammonium sulphate (3.5 g/L) at laboratory temperature for 1 hour, drying at 35 °C for 1 hour. The test usually takes 1008 hours (6 weeks).
EN ISO 12944-9
This standard deals with performance of heavy-duty paint systems designed for protection of off-shore and similar structures.
Conditions: Each week cycle includes 3-day exposure to intermittent UV irradiation (4 hours, 60 °C) and water condensation (4 hours, 50 °C) according to EN ISO 16474-3, 3-day exposure to NSS according to EN 9227 and 1-day exposure at –20 °C. Typical duration: 10, 16 or 25 weeks.
IEC 60068-2-52
A collection of cyclic corrosion test methods for environmental testing of electronic equipment and products to assess their ability to perform under environmental conditions.
Conditions: The test methods include a 2-hour salt mist (salt spray) phase using 5% NaCl (Test method 1–7) or acidified salt solution (Test method 8) at 35 °C, a humid phase at 40 °C and at 93 % RH (Test method 1–6) or at 50 °C and at 95 % RH (Test method 7, 8), and some of them also a dry phase at 23 °C and at 50 % RH (Test method 3–6) or at 60 °C and at RH > 30 % (Test method 7, 8).
Other standard or custom-defined tests can be performed upon demand.
Salt spray tests (NSS/NSST, ASS, CASS)
· EN ISO 9227
· EN ISO 13523-8
· ASTM B 117
· IEC 60068-2-11
· JIS Z 2371
· MIL-STD-810G, Test Method 509.6
· MIL-DTL-5541F
· DEF STAN 00-35, Part 3, Test CN2
· ASTM G 85, Practice A1 (AAS)
· DIN 50021 (invalid)
· EN ISO 7253 (invalid)
· BS 7479 (invalid)
· NF X41-002 (invalid)
NSS (5 wt.% solution of NaCl at pH 6.5–7.2 sprayed continuously over sample surface) is the oldest and still most widely used accelerated test recommended for corrosion assessment of metals and alloys, metallic coatings, conversion layers and organic coatings on metal substrates. ASS (5 wt.% NaCl acidified by acetic acid to pH 3.1–3.3) and CASS (further addition of cupper (II) chloride) are used for decorative coatings of copper, nickel and chrome or nickel and chrome and coated aluminium.
Sulfur dioxide (SO2) test in a humid atmosphere(Kesternich test) 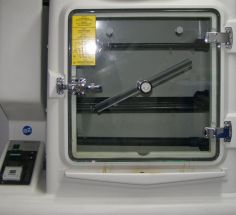
· EN ISO 22479
· EN ISO 13523-23
· ASTM G87
· EN 60086-2-42
· DIN 50018 (DIN 50018 - 1,0 S, DIN 50018 - 2,0 S, DIN 50018 - KFW 1,0 S, DIN 50018 - KFW 2,0 S, DIN 50018 - AHT 1,0 S, DIN 50018 - AHT 2,0 S)
· ISO 6988 (invalid)
· ISO 3231 (invalid)
Kesternich testing (determination of resistance to humid atmospheres containing sulfur dioxide) was originally developed to model exposures of painted metals to industrially polluted atmospheres. Due to high sulphur dioxide concentrations, the correlation between results of field and Kesternich tests is limited. However, the SO2 tests proved to highlight efficiently presence of pores and other defects in organic and metallic coatings and their use has thus been growing in past years.
Conditions: Parts or panels with the total surface area of 0.5 m2 are placed inside a 300-litre chamber where 0.2, 1 or 2 litres of SO2 is introduced or generated and high humidity (condensation conditions) maintained for 8 hours. According to Method B, these periods are alternated with 16-hour repose at laboratory temperature at at relative humidity close to 50 %. When Method A is used, no drying is applies. A cycle takes 24 hours. Test duration is 1, 2, 5, 10, 15, 20 or more daily cycles.
Other corrosion tests
EN ISO 12944
Procedures for performance testing of painted steel structures aimed for application in atmosphere with defined corrosivity are described. It is described here.
IEC 61646, Part 10.12
The procedure is similar to PV 1200. It was developed for photovoltaic panels but can be used as a very tough test of paint stability in view of adhesion and tendency to blistering.
Conditions: The test comprises at least ten 24-hour cycles at 85 % RH with the temperature varying between laboratory temperature, 85 °C, and –40 °C with two rates of cooling and heating at 100 and 200 °C per hour.
DEF STAN 00-35, Part 3, Test CN3
This test is applicable to materiel which is liable to be exposed to acidic atmospheres, particularly when deployed in industrial areas or near exhausts of any fuel burning appliance.
Conditions: The test procedure is comprised of test cycles each consisting of 2 hours exposure to an acid-laden atmosphere and a period of storage at 40 °C and 93 % RH.
DEF STAN 00-35, Part 3, Test CN4
The test is intended to determine the response of materiel to any potentially damaging effects of contaminating fluids such as fuels, oils, solvents, cleaning fluids, disinfectants, etc.
For weathering and climatic tests (degradation by UV and other climatic factors), click here.
We can help with selection of the optimal procedure in view of the required product or structure lifetime and service conditions.
We provide complete service including sample preparation, intermediate evaluations, e.g. for the assessment of time to red rust appearance, final evaluation and documentation of actual test conditions. The extent of intermediate and final assessment can be tailored according to the customer needs, following standards such as EN ISO 4628 on the evaluation of degradation of organic coatings (rusting, cracking, chalking, blistering, flaking, filiform corrosion, delamination), or particular customary procedures. Our analytical, electrochemical, metallographic and other equipment allows for in-detail analysis of corrosion degradation in terms of uniformity, mean and maximal pit depth, composition of corrosion products, paint delamination morphology and mechanism, paint adhesion (EN ISO 2409, ASTM D3359), paint water uptake, hem flange corrosion, etc.
![]() |
![]() |
![]() |
In addition to standard tests, we offer the possibility to develop customary tests according to your specific needs. A battery of dc and ac electrochemical methods and immersion tests in combination with procedures listed above constitute a strong basis for proper assessment of material stability.
Service data are often required for confirmation of laboratory results. We oversee field exposures at well-managed natural weathering sites in the Czech Republic and other European countries, USA, China and elsewhere. The accelerated outdoor test by intermittent spraying of a salt solution according to ISO 11474, the SCAB (Simulated Corrosion Atmospheric Breakdown) test, can also be carried out.
Accelerated corrosion testing will help you reducing detrimental effects of corrosion. | ![]() |
About us
Technopark Kralupy is a spin-off of The University of Chemistry and Technology Prague serving the Czech and international industry in the field of building chemistry and similar subjects since 2015.
Contact
Department of Metallic Construction Materials
Technopark Kralupy of the University of Chemistry and Technology Prague
Technopark Kralupy VŠCHT Praha
Náměstí G. Karse 7
278 01 Kralupy nad Vltavou
Czech Republic
kovy@technopark-kralupy.cz
Phone: +420 220 446 104, +420 723 242 413
© 2017–2025 Technopark Kralupy